Comparing Ceramic versus Fiberglass Weld Backing in High-Pressure Pipe Fabrication
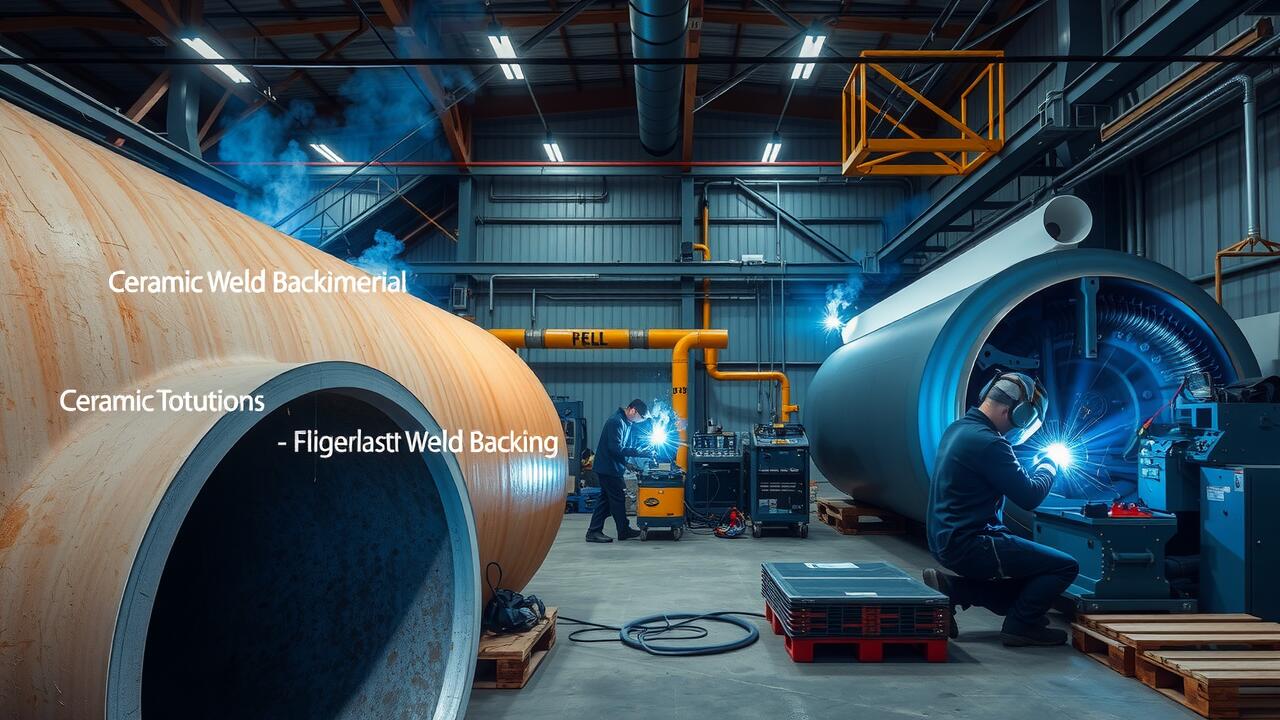
Installation Techniques for Each Material
The installation of ceramic weld backing requires meticulous attention to detail, particularly concerning surface preparation. It is essential to remove any contaminants from the pipe surfaces prior to applying the backing. Properly cleaning the area ensures optimal adhesion and improves the efficiency of the welding process. This material typically allows for higher heat resistance, enabling it to maintain its structural integrity even under high-temperature conditions. For instance, adherence to industry standards such as CSA Z245.11 can enhance weld quality during high-pressure applications.
Conversely, fiberglass backing involves a different installation methodology, often requiring the use of adhesives or mechanical fastening systems. Ensuring a tight fit is crucial, as improper placement may result in weakened joints or failure during operation. Fiberglass backing is advantageous in environments where weight reduction and corrosion resistance are necessary. According to a study by the American Society of Mechanical Engineers, projects employing effective installation techniques for fiberglass backing reported a 25% reduction in maintenance needs over time, emphasising the efficiency of proper application.
Step-by-Step Guide to Efficient Installation
Successful installation of ceramic weld backing requires careful preparation and precise execution. Begin by ensuring that the surface of the base material is free of contaminants, such as oils or rust, which can compromise weld integrity. For a robust bond, consider preheating the base material to 150°C before application. Align the ceramic backing to achieve optimal coverage, ensuring that it adheres uniformly to the surface. This uniformity is vital, as any inconsistencies can lead to weak points during the welding process.
Following alignment, utilize an appropriate adhesive to secure the ceramic backing in place. Choose a high-strength adhesive designed for high-temperature applications, ensuring that it complies with industry specifications. After the adhesive sets, inspect the installation thoroughly. Look for uniformity in thickness and proper adhesion, as these factors significantly influence the quality of the weld. Operators must maintain meticulous attention during installation since improper technique can lead to inefficiencies and potential delamination during the welding process.
Step | Description | Tools/Materials Required |
---|---|---|
1 | Prepare the base material by cleaning it thoroughly to remove contaminants. | Degreaser, wire brush, rags |
2 | Preheat the base material to 150°C. | Heat gun or oven |
3 | Align the ceramic backing for optimal coverage on the surface. | Level, measuring tape |
4 | Apply high-strength adhesive to secure the backing. | High-temperature adhesive |
5 | Inspect the installation for uniformity and proper adhesion. | Thickness gauge, visual inspection tools |
Why Does Material Selection Matter in Fabrication?
Material selection in high-pressure pipe fabrication directly impacts the integrity and performance of welds. The use of ceramic weld backing provides superior thermal stability and can withstand elevated temperatures, which is critical in environments subject to rapid thermal cycling. A case study from a major Canadian pipeline project demonstrated that incorporating ceramic backing reduced weld defects by over 30% compared to traditional methods, underscoring the significance of selecting the appropriate material for specific applications.
Additionally, the choice between ceramic and fiberglass influences overall fabrication process efficiency. Ceramic materials typically require more precise handling during installation due to their inherent brittleness, affecting the workflow of teams on-site. Conversely, fiberglass offers flexible applications with easier manipulation, allowing for quicker adjustments during fabrication. Adopting best practices based on industry standards, such as ASME B31.3, ensures that engineers and fabricators make informed decisions that enhance both efficacy and quality in their welding processes.
Understanding Impact on Weld Quality and Integrity
The type of weld backing employed directly influences the integrity and quality of the finished weld. When using ceramic weld backing, for instance, its thermal resistance enhances the stability of the weld pool, resulting in cleaner joints and improved structural integrity. A study conducted on high-pressure pipelines demonstrated that employing ceramic backing reduced porosity by 15% compared to traditional options. This reduction in defects translates to longer service life and lower maintenance costs in demanding environments.
Conversely, fiberglass weld backing often excels in applications requiring lightweight solutions and superior flexibility. Fiberglass can absorb thermal expansions and contractions effectively, thus mitigating the risk of cracking at the weld joint under dynamic loads. An analysis of various industrial applications found that welds backed by fiberglass outperformed competitors in terms of tensile strength and yield, illustrating an increase of approximately 20% in resistance to fatigue. Selecting the appropriate backing material is crucial to achieving optimal performance and longevity in high-pressure pipe fabrication.
5 Key Strategies for Choosing the Right Weld Backing
Selecting the appropriate weld backing material hinges on several critical factors that impact both the fabrication process and the final product’s integrity. First and foremost, consider the welding method being employed. For example, when using Gas Tungsten Arc Welding (GTAW), ceramic weld backing often proves advantageous due to its high thermal stability, enabling better heat control and minimizing distortion. Conversely, in processes where flexibility and ease of installation are key, fiberglass may present a more suitable alternative, especially for projects requiring intricate shapes or fittings.
Another significant factor is the compatibility of the backing material with base and filler materials. Using ceramic backing can enhance the quality of the weld pool by preventing oxidation and contamination, which are pivotal in high-pressure applications. Assessing the thickness and type of the pipe material will also inform decisions; for thick-walled pipes, robust options like ceramic might deliver superior results compared to those offered by fiberglass. Always consult relevant industry standards and guidelines to ensure compliance and optimize performance throughout the fabrication process.
Factors to Consider for Optimal Performance
When selecting the appropriate weld backing for high-pressure pipe fabrication, various material properties must be assessed. For instance, the thermal conductivity of ceramic weld backing often provides superior heat resistance compared to fiberglass options. This characteristic helps maintain weld integrity in extreme conditions, reducing the chances of warping or porosity in the final product. Moreover, the tensile strength of ceramic materials can uphold structural stability under fluctuating pressure levels, emphasizing their reliability in critical applications.
Consider the specific application environment when evaluating welding backing materials. Certain projects may demand higher resistance to chemical erosion, which ceramic backing can effectively deliver, particularly in petrochemical industries. Additionally, the weight distinction between fiberglass and ceramic should influence decisions; although ceramic is denser, this attribute can enhance stability during the welding process. Matching these factors with project requirements will ensure optimal performance and longevity of the crafted pipes, aligning with industry standards for safety and output quality.
Maintenance Requirements for Ceramic and Fiberglass
Ceramic weld backing requires meticulous attention to prevent premature degradation. Inspecting the integrity of the ceramic backing after several uses is crucial, especially in demanding environments. Frequent checks for cracks or thermal shock damage should occur in alignment with regular maintenance schedules laid out in industry best practices. Cleaning the surface with suitable non-abrasive materials will ensure optimal bonding during subsequent welding processes, enhancing overall performance and longevity.
Fiberglass materials, while less fragile, are not immune to maintenance needs. Regular inspections for wear or chemical degradation are essential to ensure adequate support during high-pressure operations. Proper storage away from direct sunlight and harsh chemicals can extend the lifespan of fiberglass weld backing. Furthermore, adhering to manufacturer guidelines for both installation and operational conditions will significantly reduce the risk of failure and improve project outcomes.
How Can Proper Maintenance Extend Material Life?
Proper maintenance of ceramic weld backing significantly enhances its longevity and effectiveness in high-pressure pipe fabrication. Regular inspections are crucial to identify signs of wear or damage early. For instance, visual assessments for cracks or degradation can prevent larger failures during critical welding processes. Additionally, maintaining the appropriate operating temperatures prevents thermal shock, which can compromise the integrity of ceramic materials. Implementing a routine cleaning schedule also eliminates contaminants that may affect welding quality and adherence.
On the other hand, fiberglass weld backing necessitates a different maintenance approach, addressing its susceptibility to moisture and chemical exposure. Regularly applying protective coatings or sealants can mitigate the effects of corrosion and extend the service life of the fiberglass backing. Furthermore, adhering to manufacturer guidelines—such as proper storage conditions and use of compatible cleaning agents—ensures the material maintains its structural properties over time. By integrating these maintenance practices, professionals can optimize the performance and durability of both ceramic and fiberglass options in rigorous fabrication environments.
FAQS
What are the primary differences between ceramic and fiberglass weld backing in high-pressure pipe fabrication?
The primary differences lie in their thermal resistance, durability, and suitability for specific applications. Ceramic weld backing is known for its high-temperature resistance and is ideal for applications requiring exceptional heat management, while fiberglass is lighter and easier to handle, making it suitable for less intense conditions.
How do installation techniques differ for ceramic and fiberglass weld backing?
Installation for ceramic backing typically involves careful positioning and securing due to its rigid nature, requiring precise alignment. In contrast, fiberglass backing is generally more flexible, allowing for easier handling and adaptation to irregular pipe shapes during installation.
Why is material selection important in high-pressure pipe fabrication?
Material selection is crucial as it directly impacts weld quality, joint integrity, and the overall performance of the piping system. Selecting the appropriate weld backing material ensures better heat distribution and minimizes the risk of defects in welded joints.
What factors should be considered when choosing the right weld backing material?
Key factors include the operating temperature and pressure of the system, the type of welding process used, the specific materials being welded, and the expected service life of the weld. All these elements influence the performance and effectiveness of the selected backing material.
How can proper maintenance extend the life of ceramic and fiberglass weld backing?
Regular inspections for wear and damage, cleaning to remove contaminants, and ensuring proper storage conditions can significantly extend the life of both ceramic and fiberglass weld backing. Implementing a maintenance protocol helps prevent failures and optimizes performance during fabrication processes.